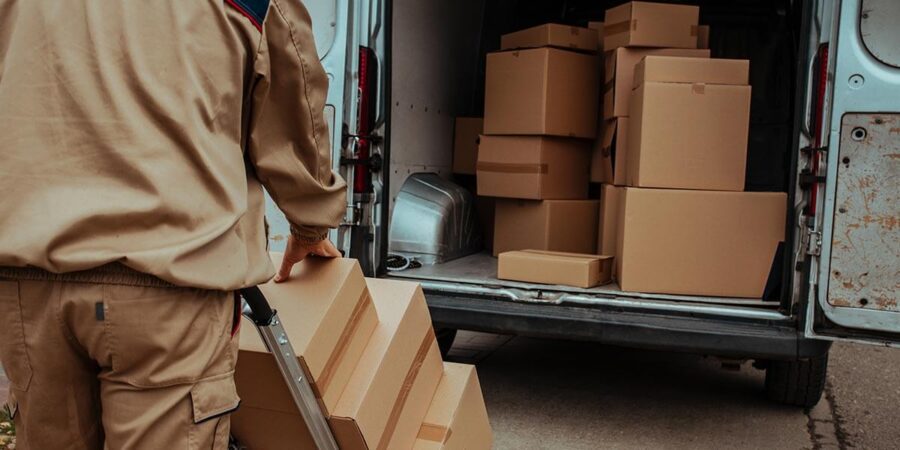
Carrier
Can Automating Return Fulfilment Solve the Reverse Logistics Equation?
Written by: Parcel Pending
3 Min Read
Published: February 7, 2023
Updated: October 26, 2023
According to a recent Shopify report, returns account for an average of 20-30% of online orders, highlighting the upward trend of returns stemming from online sales.1 This rapid growth in merchandise returns is leaving carriers seeking ways to alleviate the mounting pressure to scale to added first-mile activity and the rising costs associated with it. The extra activity underscores areas where carriers need to recalibrate business operations and improve out of home strategies – including reducing the number of driver stops, lowering fuel costs, and meeting sustainability objectives.
Consolidating first and last mile deliveries to centralised smart lockers can have a positive effect on the return process. Carriers need to automate fulfilment options to improve business operations, help drive down the costs of processing returns, and create a competitive advantage.
Critical to realising the efficiency gains of smart lockers is keeping the customer top of mind in the operation. Lockers offer a self-service option for customers that will be utilised if it is convenient. This convenience can be realised by locating the locker in a frequently visited location, making it available for both pick-ups and returns, enabling locker access 24/7, etc. Enabling such convenience drives adoption and helps to realise consolidation of first and last-mile delivery activity.
Introducing Drop Box
The latest addition to the Parcel Pending by Quadient product roster is our fully integrated Drop Box with optional Printer solution. This first of its kind solution was developed to suit various use cases with an option for one printer to enhance our existing ability to fulfil returned merchandise through our lockers. The printer enables consumers to print authentic shipping labels from our outdoor lockers at the drop-off site. This means drivers no longer have to print and stick labels. Returned packages are dropped into drop off lockers, maximising parcel volume while minimising the locker footprint. Our Track and Trace technology captures every step of the return process from start to pick up and can be monitored from our cloud-based locker management system.
All of our solutions are fully integrated with Quadient’s centralised locker management system. Our cloud-based system provides monitoring in real-time, delivering the information carriers need when and where it’s needed. Carriers can gain key insights from actionable data such as: the amount of time from a return request to drop off, locker availability and usage, pick-up and drop-off alerts, track and trace, business intelligence reports, and more.
Parcel Pending by Quadient worked closely with carriers and our retail customers in Europe, the United States and Japan to develop our unique line of Drop Box lockers. Our Drop Box lockers can be added to our existing locker systems or custom configured for new installations to automate fulfilment of returned merchandise.
Automating return fulfilment through Quadient’s advanced parcel fulfilment solution, our Drop Box with printer, can bring the operational efficiencies by:
- Eliminating the need for drivers to print labels
- Consolidating multiple stops to a single pick-up, drop-off point
- Shaving valuable time off first mile logistics to get drivers back on the road
Alleviate the time-consuming manual processes of first mile logistics and improve your bottom line. Learn more about Parcel Pending by Quadient Drop Box lockers.
Sources:
- Dopson, Elise. Ecommerce Returns: Expert Guide to Best Practices. www.shopify.com. August 25, 2021. https://www.shopify.com/enterprise/ecommerce-returns